Intro
Explore the alarming rise of faulty welds at Newport News Shipyard, a concern threatening maritime safety and naval operations. Discover the causes, consequences, and potential solutions to this growing issue, including weld inspection, quality control, and regulatory compliance. Get informed on this critical topic affecting shipbuilding and repair industries.
The Newport News Shipyard, one of the largest and most respected shipyards in the world, has been facing a growing concern in recent years: faulty welds. This issue has significant implications for the safety and reliability of the ships and submarines built at the yard, as well as for the reputation of the shipyard itself.
The importance of weld quality cannot be overstated. Welds are a critical component of ship construction, providing the structural integrity necessary to withstand the stresses and strains of the marine environment. Faulty welds, on the other hand, can lead to a range of problems, including leaks, cracks, and even catastrophic failures. As such, ensuring the quality of welds is a top priority for shipbuilders and naval architects.
Despite its reputation for excellence, the Newport News Shipyard has been plagued by issues with faulty welds in recent years. This problem has been identified in a number of different areas, including the construction of nuclear-powered aircraft carriers and submarines. In some cases, the faulty welds have been attributed to inadequate training and certification of welders, while in others, they have been linked to the use of substandard materials or equipment.
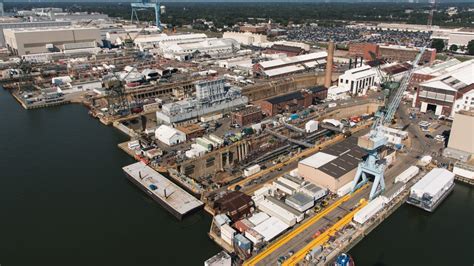
Causes of Faulty Welds
There are a number of factors that can contribute to faulty welds, including:
1. Inadequate Training and Certification
Welding is a highly skilled trade that requires extensive training and certification. However, in recent years, there have been concerns that some welders at the Newport News Shipyard may not have received adequate training or certification.
2. Substandard Materials or Equipment
The use of substandard materials or equipment can also contribute to faulty welds. This can include everything from low-quality welding rods to inadequate shielding gases.
3. Insufficient Quality Control
Finally, insufficient quality control measures can also contribute to faulty welds. This can include inadequate inspection and testing procedures, as well as a lack of accountability among welders and supervisors.
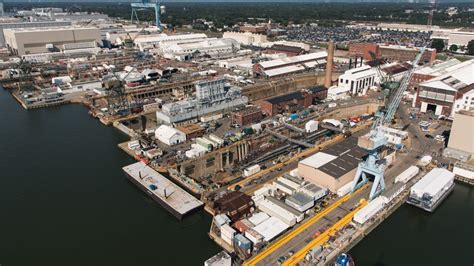
Consequences of Faulty Welds
The consequences of faulty welds can be severe and far-reaching. Some of the most significant consequences include:
1. Safety Risks
Faulty welds can pose significant safety risks to the crew and passengers of ships and submarines. Leaks, cracks, and other failures can lead to flooding, fires, and other hazards.
2. Cost Overruns
Faulty welds can also lead to significant cost overruns. Repairing or replacing faulty welds can be a time-consuming and expensive process, especially if it requires dry-docking a ship or submarine.
3. Reputation Damage
Finally, faulty welds can damage the reputation of the Newport News Shipyard and the U.S. Navy. This can have long-term consequences for the yard's ability to attract new contracts and customers.

Solutions to Faulty Welds
Fortunately, there are a number of solutions to the problem of faulty welds at the Newport News Shipyard. Some of the most effective solutions include:
1. Improved Training and Certification
Improving the training and certification of welders is a critical step in addressing the problem of faulty welds. This can include providing additional training and certification programs for welders, as well as ensuring that all welders meet strict quality control standards.
2. Enhanced Quality Control Measures
Enhancing quality control measures is also essential for addressing the problem of faulty welds. This can include implementing more rigorous inspection and testing procedures, as well as increasing accountability among welders and supervisors.
3. Investment in New Technology
Finally, investing in new technology can also help to address the problem of faulty welds. This can include the use of advanced welding equipment and techniques, such as robotic welding and advanced non-destructive testing methods.
Newport News Shipyard Welding Image Gallery
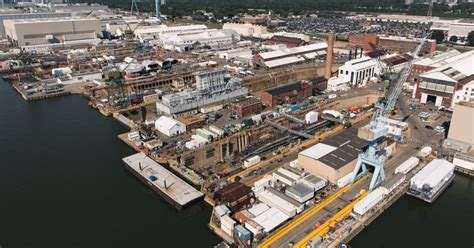
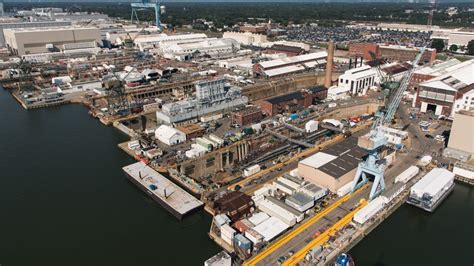

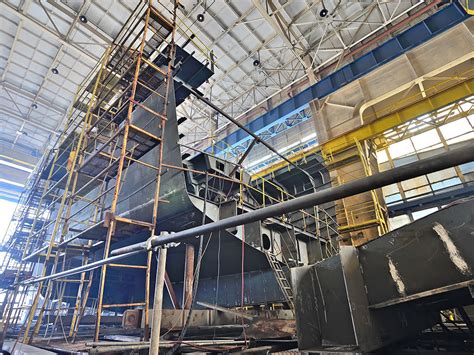

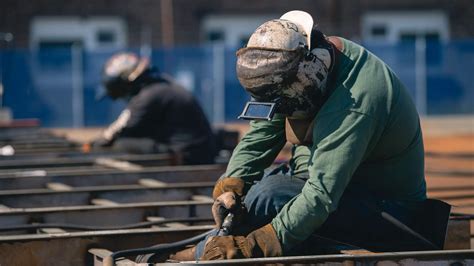
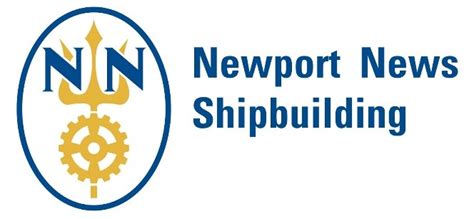
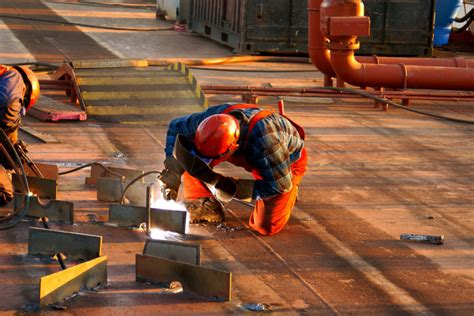
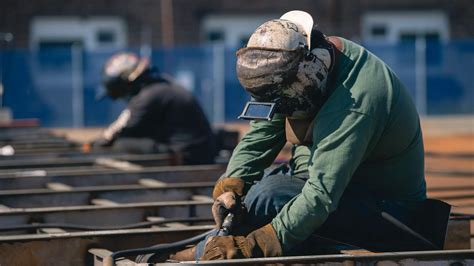
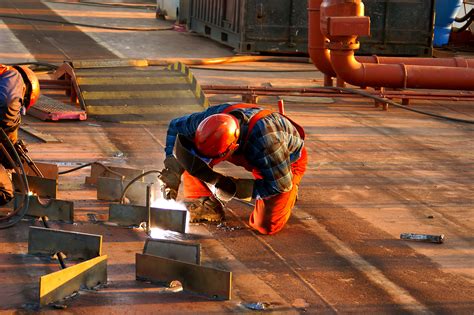
What is the cause of faulty welds at the Newport News Shipyard?
+The cause of faulty welds at the Newport News Shipyard is attributed to inadequate training and certification of welders, substandard materials or equipment, and insufficient quality control measures.
What are the consequences of faulty welds?
+The consequences of faulty welds include safety risks, cost overruns, and reputation damage to the Newport News Shipyard and the U.S. Navy.
What solutions can address the problem of faulty welds?
+Solutions to address the problem of faulty welds include improving training and certification of welders, enhancing quality control measures, and investing in new technology.
We hope this article has provided valuable insights into the issue of faulty welds at the Newport News Shipyard. As the shipyard continues to work towards addressing this problem, it is essential for all stakeholders to be aware of the causes, consequences, and solutions to this critical issue. By working together, we can ensure the safety and reliability of our ships and submarines, and maintain the reputation of the Newport News Shipyard as a world-class shipbuilding facility.