Intro
Discover the 5 most common weld issues in Navy shipyards, including porosity, lack of fusion, and inadequate penetration. Learn how to identify and prevent these defects, ensuring the structural integrity of naval vessels. Expert insights and solutions for welding professionals to improve shipyard quality and safety.
Welding is a crucial process in the construction and maintenance of naval vessels. In a navy shipyard, welding is used to join various metals and alloys to build and repair ships, submarines, and other marine equipment. However, like any other manufacturing process, welding can be prone to errors and defects. In this article, we will discuss five common weld issues that can occur in a navy shipyard and their causes, effects, and possible solutions.
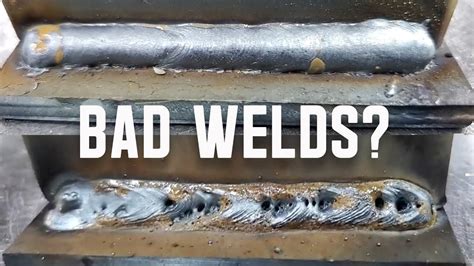
Porosity in Welds
Porosity in welds is a common issue that can occur in navy shipyards. Porosity refers to the formation of small holes or cavities in the weld metal. This can happen due to various reasons, including:
- Insufficient shielding gas coverage
- High welding speeds
- Incorrect welding technique
- Contamination of the weld area
Porosity can weaken the weld joint and make it more susceptible to corrosion. In a navy shipyard, porosity can have serious consequences, including:
- Reduced structural integrity of the ship
- Increased risk of leakage or flooding
- Higher maintenance costs
To prevent porosity, welders can use proper shielding gas coverage, adjust their welding technique, and ensure that the weld area is clean and free from contamination.
Causes of Porosity
- Insufficient shielding gas coverage
- High welding speeds
- Incorrect welding technique
- Contamination of the weld area
Effects of Porosity
- Weakened weld joint
- Increased risk of corrosion
- Reduced structural integrity of the ship
- Increased risk of leakage or flooding
- Higher maintenance costs
Solutions to Prevent Porosity
- Use proper shielding gas coverage
- Adjust welding technique
- Ensure clean and free weld area
- Use proper welding equipment and consumables
Lack of Fusion
Lack of fusion is another common weld issue that can occur in navy shipyards. Lack of fusion refers to the failure of the weld metal to melt and fuse with the base metal. This can happen due to various reasons, including:
- Insufficient heat input
- Incorrect welding technique
- Poor joint preparation
- Inadequate shielding gas coverage
Lack of fusion can lead to a weak weld joint that is prone to cracking and failure. In a navy shipyard, lack of fusion can have serious consequences, including:
- Reduced structural integrity of the ship
- Increased risk of leakage or flooding
- Higher maintenance costs
To prevent lack of fusion, welders can use proper welding technique, ensure adequate heat input, and prepare the joint properly.
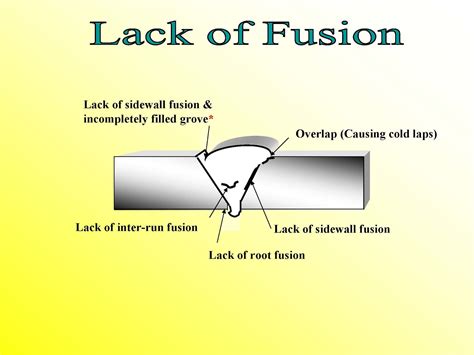
Causes of Lack of Fusion
- Insufficient heat input
- Incorrect welding technique
- Poor joint preparation
- Inadequate shielding gas coverage
Effects of Lack of Fusion
- Weak weld joint
- Increased risk of cracking and failure
- Reduced structural integrity of the ship
- Increased risk of leakage or flooding
- Higher maintenance costs
Solutions to Prevent Lack of Fusion
- Use proper welding technique
- Ensure adequate heat input
- Prepare joint properly
- Use proper shielding gas coverage
Weld Cracks
Weld cracks are a common issue that can occur in navy shipyards. Weld cracks refer to the formation of cracks in the weld metal or heat-affected zone (HAZ). This can happen due to various reasons, including:
- High residual stresses
- Poor welding technique
- Inadequate post-weld heat treatment (PWHT)
- Material defects
Weld cracks can lead to a weak weld joint that is prone to failure. In a navy shipyard, weld cracks can have serious consequences, including:
- Reduced structural integrity of the ship
- Increased risk of leakage or flooding
- Higher maintenance costs
To prevent weld cracks, welders can use proper welding technique, ensure adequate PWHT, and inspect the weld joint regularly.
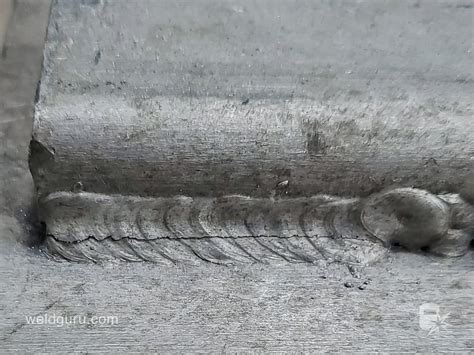
Causes of Weld Cracks
- High residual stresses
- Poor welding technique
- Inadequate post-weld heat treatment (PWHT)
- Material defects
Effects of Weld Cracks
- Weak weld joint
- Increased risk of failure
- Reduced structural integrity of the ship
- Increased risk of leakage or flooding
- Higher maintenance costs
Solutions to Prevent Weld Cracks
- Use proper welding technique
- Ensure adequate PWHT
- Inspect weld joint regularly
- Use proper welding equipment and consumables
Distortion and Warping
Distortion and warping are common issues that can occur in navy shipyards. Distortion and warping refer to the uneven heating and cooling of the weld metal and surrounding base metal, leading to changes in the shape and dimensions of the weld joint. This can happen due to various reasons, including:
- High heat input
- Poor welding technique
- Inadequate fixture and clamping
- Material defects
Distortion and warping can lead to a weak weld joint that is prone to failure. In a navy shipyard, distortion and warping can have serious consequences, including:
- Reduced structural integrity of the ship
- Increased risk of leakage or flooding
- Higher maintenance costs
To prevent distortion and warping, welders can use proper welding technique, ensure adequate fixture and clamping, and inspect the weld joint regularly.
Causes of Distortion and Warping
- High heat input
- Poor welding technique
- Inadequate fixture and clamping
- Material defects
Effects of Distortion and Warping
- Weak weld joint
- Increased risk of failure
- Reduced structural integrity of the ship
- Increased risk of leakage or flooding
- Higher maintenance costs
Solutions to Prevent Distortion and Warping
- Use proper welding technique
- Ensure adequate fixture and clamping
- Inspect weld joint regularly
- Use proper welding equipment and consumables
Corrosion
Corrosion is a common issue that can occur in navy shipyards. Corrosion refers to the degradation of the weld metal and surrounding base metal due to chemical or electrochemical reactions with the environment. This can happen due to various reasons, including:
- Inadequate surface preparation
- Poor welding technique
- Inadequate post-weld treatment (PWT)
- Exposure to corrosive environments
Corrosion can lead to a weak weld joint that is prone to failure. In a navy shipyard, corrosion can have serious consequences, including:
- Reduced structural integrity of the ship
- Increased risk of leakage or flooding
- Higher maintenance costs
To prevent corrosion, welders can use proper surface preparation, ensure adequate PWT, and inspect the weld joint regularly.
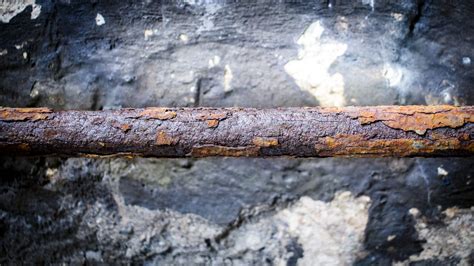
Causes of Corrosion
- Inadequate surface preparation
- Poor welding technique
- Inadequate post-weld treatment (PWT)
- Exposure to corrosive environments
Effects of Corrosion
- Weak weld joint
- Increased risk of failure
- Reduced structural integrity of the ship
- Increased risk of leakage or flooding
- Higher maintenance costs
Solutions to Prevent Corrosion
- Use proper surface preparation
- Ensure adequate PWT
- Inspect weld joint regularly
- Use proper welding equipment and consumables
Welding Issues in Navy Shipyard Image Gallery
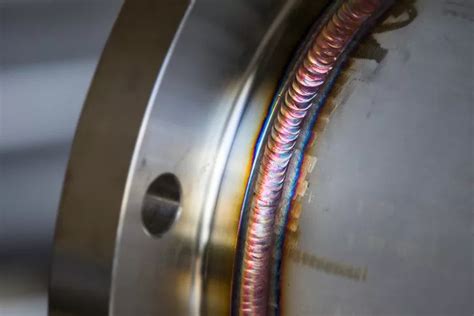
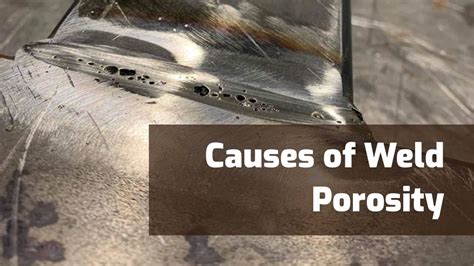
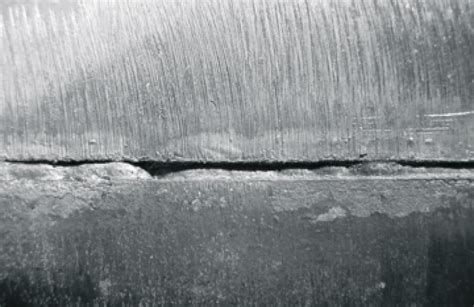
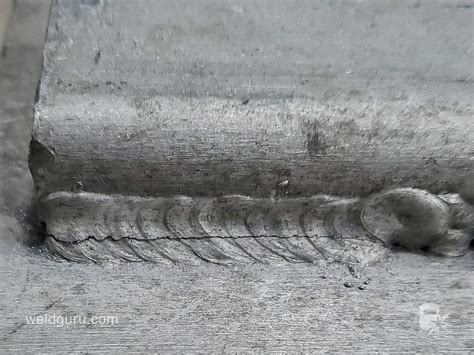
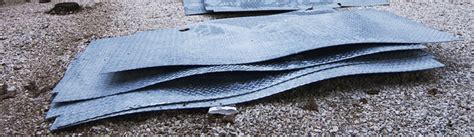
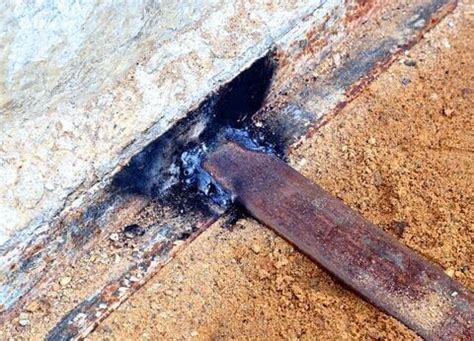
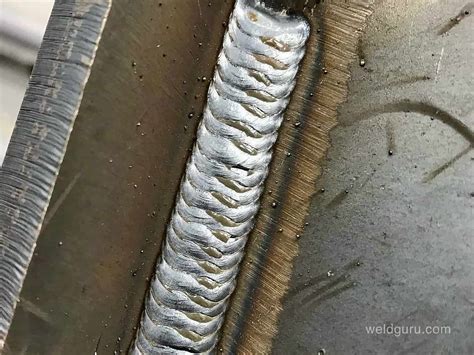
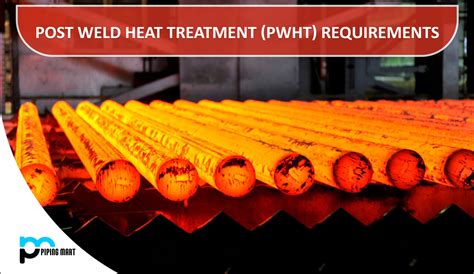
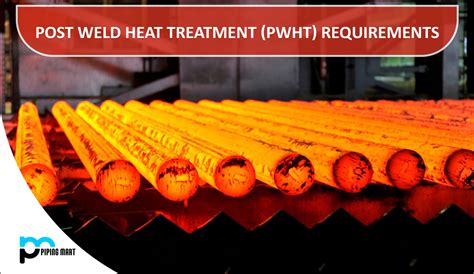
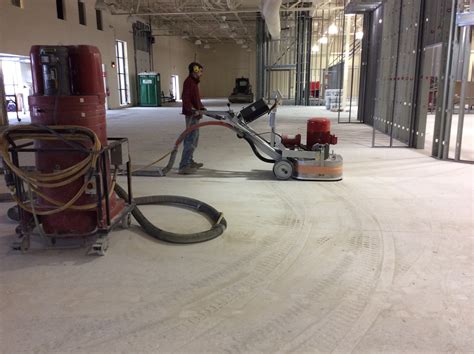
What are the common weld issues in a navy shipyard?
+The common weld issues in a navy shipyard include porosity, lack of fusion, weld cracks, distortion and warping, and corrosion.
What causes porosity in welds?
+Porosity in welds can be caused by insufficient shielding gas coverage, high welding speeds, incorrect welding technique, and contamination of the weld area.
How can weld cracks be prevented?
+Weld cracks can be prevented by using proper welding technique, ensuring adequate post-weld heat treatment (PWHT), and inspecting the weld joint regularly.
What is the effect of corrosion on welds?
+Corrosion can weaken the weld joint and increase the risk of failure, reducing the structural integrity of the ship and increasing the risk of leakage or flooding.
How can distortion and warping be prevented?
+Distortion and warping can be prevented by using proper welding technique, ensuring adequate fixture and clamping, and inspecting the weld joint regularly.
We hope this article has provided valuable information on the common weld issues that can occur in a navy shipyard. By understanding the causes, effects, and solutions to these issues, welders and engineers can take steps to prevent them and ensure the structural integrity of naval vessels. Remember to share your thoughts and experiences in the comments section below.