Intro
Discover how faulty welds can compromise the integrity of ships built at Newport News Shipyard. Learn about the 5 critical ways welding defects impact naval vessel performance, safety, and maintenance costs. From structural weaknesses to corrosion risks, explore the consequences of subpar welding and the importance of quality assurance in shipbuilding.
Newport News Shipyard, one of the largest and most renowned shipyards in the world, has been at the forefront of shipbuilding and repair for over a century. With a long history of producing some of the most advanced naval vessels and submarines, the shipyard's commitment to quality and excellence is evident in every aspect of its operations. However, like any complex industrial process, shipbuilding is not immune to errors or defects, including faulty welds. In this article, we will explore the potential consequences of faulty welds on the Newport News Shipyard's operations, products, and reputation.
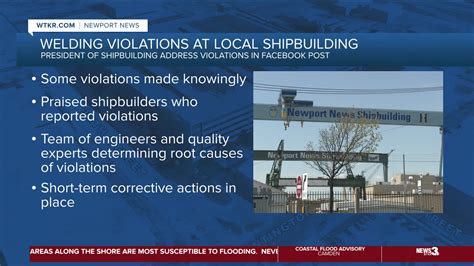
The Impact on Product Quality and Performance
Faulty welds can have a significant impact on the quality and performance of the ships and submarines built at Newport News Shipyard. A faulty weld can compromise the structural integrity of the vessel, leading to a range of problems, including:
- Reduced strength and durability
- Increased risk of leaks and water ingress
- Decreased resistance to corrosion and fatigue
- Potential for catastrophic failure in extreme conditions
These defects can not only affect the performance of the vessel but also put the lives of its crew and passengers at risk. Furthermore, faulty welds can lead to costly repairs and maintenance, which can be time-consuming and resource-intensive.
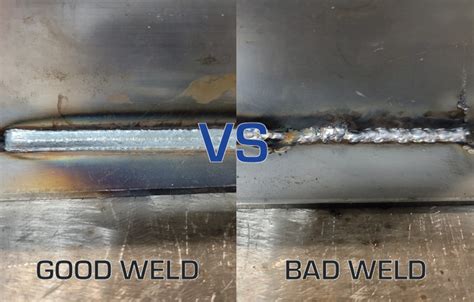
The Financial Consequences of Faulty Welds
The financial consequences of faulty welds can be significant, not only for Newport News Shipyard but also for its clients and stakeholders. Some of the potential financial impacts include:
- Costly repairs and maintenance
- Loss of productivity and efficiency
- Damage to reputation and credibility
- Potential for legal claims and liabilities
In addition to these direct costs, faulty welds can also lead to indirect costs, such as the loss of business and revenue due to delays or cancellations.
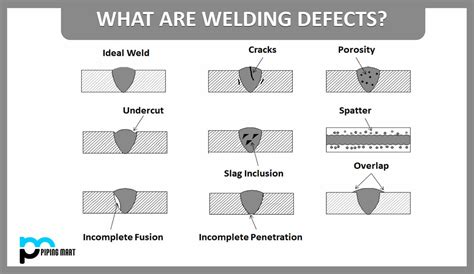
The Impact on Safety and Regulatory Compliance
Faulty welds can also have significant safety and regulatory implications for Newport News Shipyard. Some of the potential risks include:
- Non-compliance with safety and regulatory standards
- Increased risk of accidents and injuries
- Potential for fines and penalties
- Damage to reputation and credibility
In addition to these risks, faulty welds can also lead to delays and disruptions in the shipbuilding process, which can have a ripple effect throughout the entire supply chain.
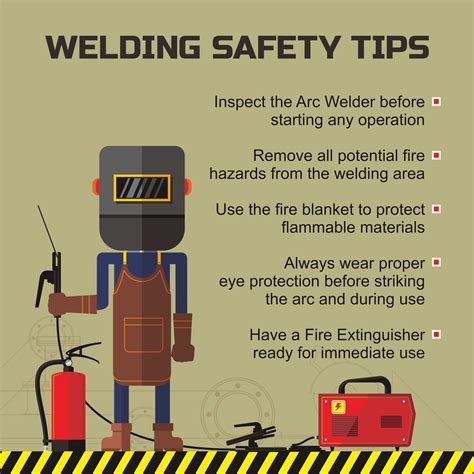
The Impact on Employee Morale and Productivity
Faulty welds can also have a significant impact on employee morale and productivity at Newport News Shipyard. Some of the potential effects include:
- Decreased job satisfaction and engagement
- Increased stress and anxiety
- Decreased productivity and efficiency
- Potential for turnover and retention issues
In addition to these effects, faulty welds can also lead to a lack of trust and confidence in the shipbuilding process, which can have long-term consequences for employee morale and productivity.
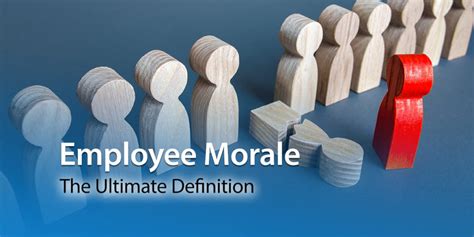
The Importance of Quality Control and Assurance
Given the potential consequences of faulty welds, it is essential that Newport News Shipyard has robust quality control and assurance processes in place. Some of the key strategies include:
- Implementing rigorous inspection and testing protocols
- Providing ongoing training and development for welders and quality control personnel
- Conducting regular audits and assessments of quality control processes
- Encouraging a culture of quality and excellence throughout the organization
By prioritizing quality control and assurance, Newport News Shipyard can minimize the risk of faulty welds and ensure that its products meet the highest standards of quality and performance.
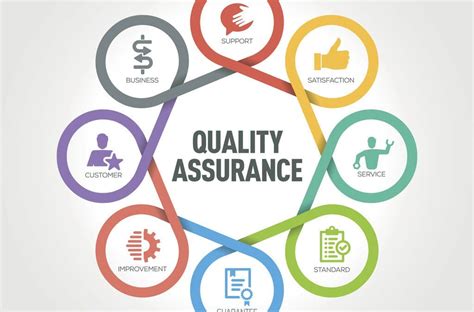
Gallery of Faulty Welds in Shipbuilding
Faulty Welds in Shipbuilding Image Gallery
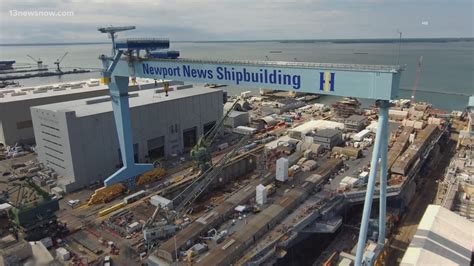
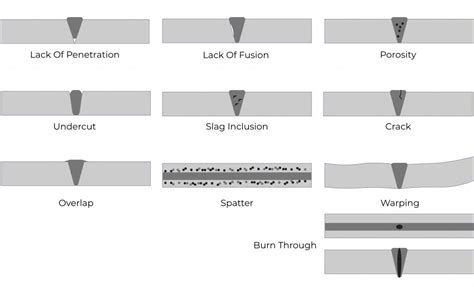
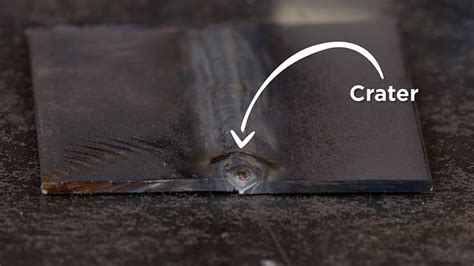
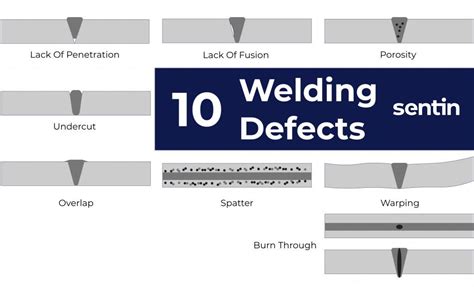
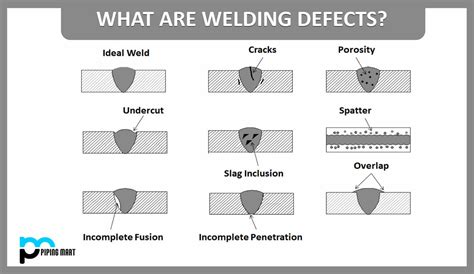
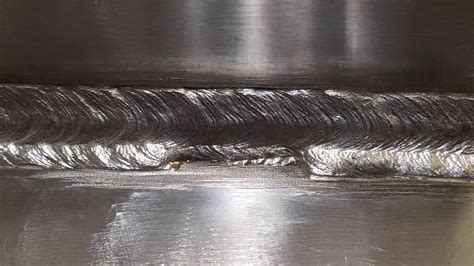
Frequently Asked Questions
What are the causes of faulty welds in shipbuilding?
+The causes of faulty welds in shipbuilding can include inadequate training, poor quality control, and insufficient inspection and testing protocols.
What are the consequences of faulty welds in shipbuilding?
+The consequences of faulty welds in shipbuilding can include reduced product quality, increased risk of accidents and injuries, and potential for costly repairs and maintenance.
How can faulty welds be prevented in shipbuilding?
+Faulty welds can be prevented in shipbuilding by implementing robust quality control and assurance processes, providing ongoing training and development for welders and quality control personnel, and conducting regular audits and assessments of quality control processes.
Final Thoughts
In conclusion, faulty welds can have significant consequences for Newport News Shipyard, including reduced product quality, increased risk of accidents and injuries, and potential for costly repairs and maintenance. By prioritizing quality control and assurance, implementing robust inspection and testing protocols, and providing ongoing training and development for welders and quality control personnel, the shipyard can minimize the risk of faulty welds and ensure that its products meet the highest standards of quality and performance.