Intro
Unlock the secrets of 3D printing a Lockheed engine in 3 groundbreaking steps. Discover the revolutionary technology and innovative techniques behind this pioneering achievement. Learn how additive manufacturing is transforming aerospace engineering with unprecedented speed and precision, leveraging advanced materials and software to push the boundaries of innovation.
The world of 3D printing has been abuzz with excitement as Lockheed Martin, a leading aerospace and defense company, has successfully printed a titanium engine component for the F-35 fighter jet. This breakthrough achievement demonstrates the vast potential of 3D printing in revolutionizing the manufacturing process of complex aerospace components.
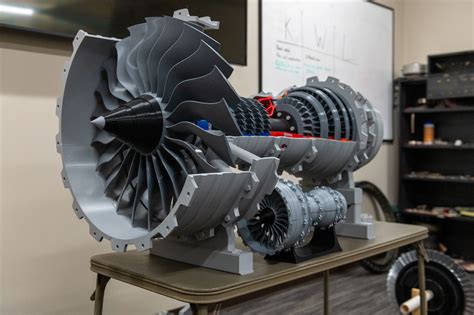
The significance of this achievement lies in the fact that it marks a major milestone in the adoption of 3D printing technology in the aerospace industry. The ability to print complex components with high precision and accuracy opens up new avenues for innovation and cost reduction.
Understanding the Challenges of Traditional Manufacturing
Traditional manufacturing methods involve the use of molds, casts, and other tools to shape materials into desired forms. However, this process can be time-consuming, expensive, and often results in significant material waste. In the aerospace industry, where precision and accuracy are paramount, traditional manufacturing methods can be particularly challenging.
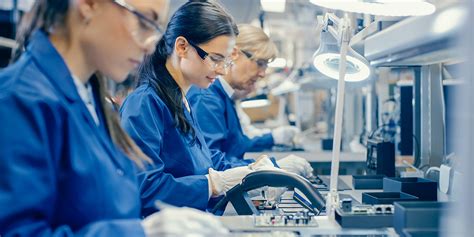
In contrast, 3D printing offers a more efficient and cost-effective solution. By building components layer by layer, 3D printing eliminates the need for molds and casts, reducing material waste and energy consumption.
The 3-Step Process of 3D Printing Lockheed Engine Components
So, how did Lockheed Martin achieve this breakthrough? The process involved three critical steps:
Step 1: Design and Simulation
The first step involved designing and simulating the engine component using advanced computer-aided design (CAD) software. This allowed the team to optimize the component's design for 3D printing, taking into account factors such as material properties, stress, and thermal performance.
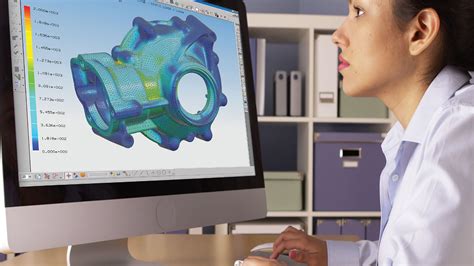
Step 2: Printing and Post-Processing
The second step involved printing the component using a high-performance 3D printer. The printer used a titanium alloy powder, which was melted and fused together layer by layer to form the desired shape. After printing, the component underwent post-processing treatments, including machining and surface finishing, to achieve the required precision and accuracy.
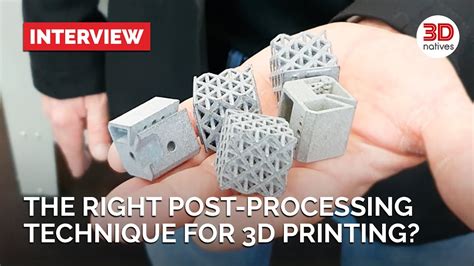
Step 3: Inspection and Testing
The final step involved inspecting and testing the printed component to ensure it met the required specifications and standards. This included non-destructive testing (NDT) techniques, such as X-ray computed tomography (CT) scanning, to verify the component's internal structure and integrity.
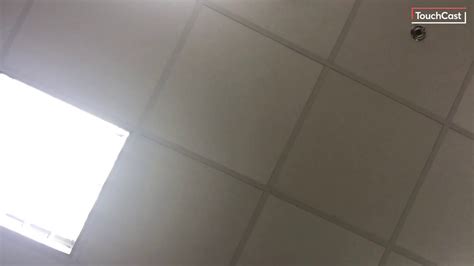
The Benefits of 3D Printing Lockheed Engine Components
The successful printing of the titanium engine component demonstrates the numerous benefits of 3D printing in the aerospace industry. These benefits include:
- Reduced material waste and energy consumption
- Increased precision and accuracy
- Improved component performance and reliability
- Reduced production time and cost
- Enhanced innovation and design flexibility
3D Printing Lockheed Engine Gallery
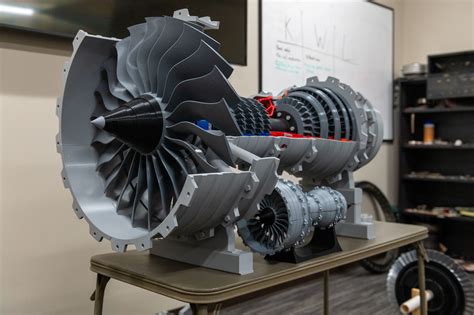
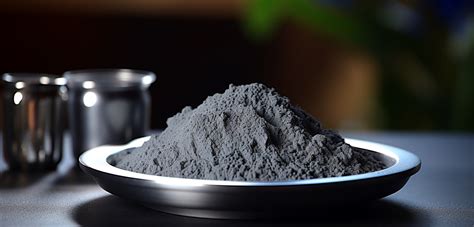
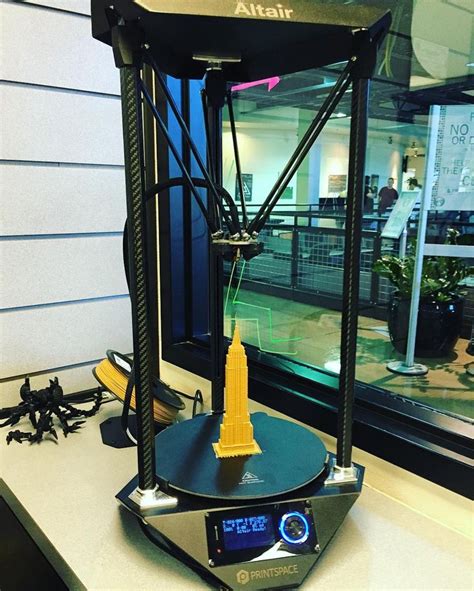
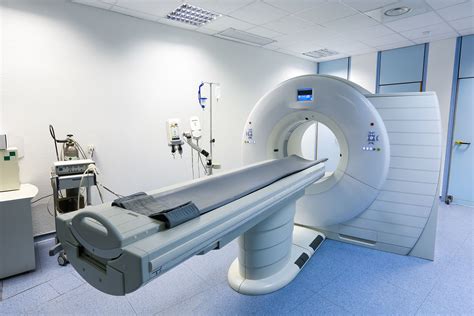
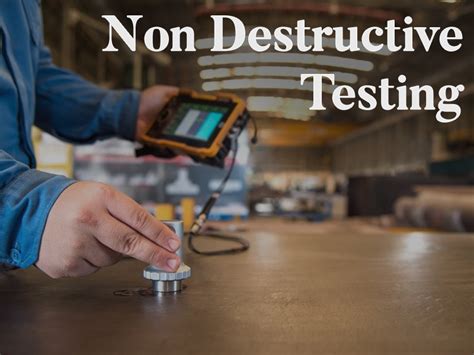
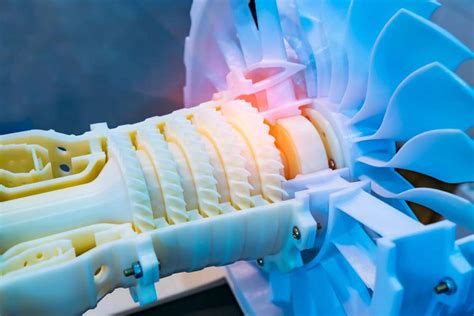
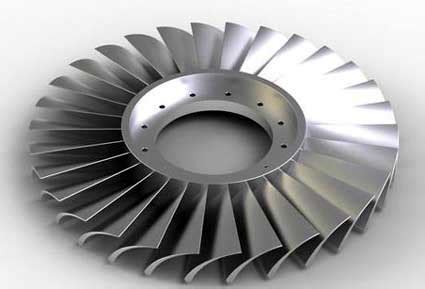
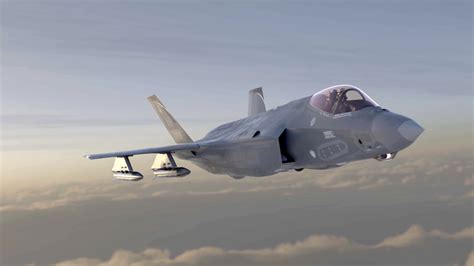
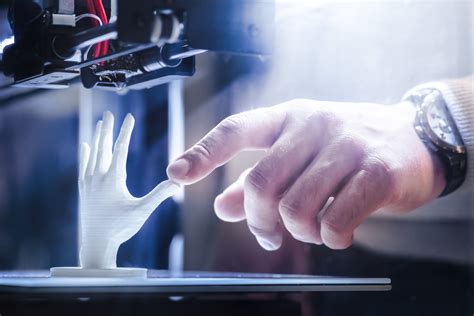
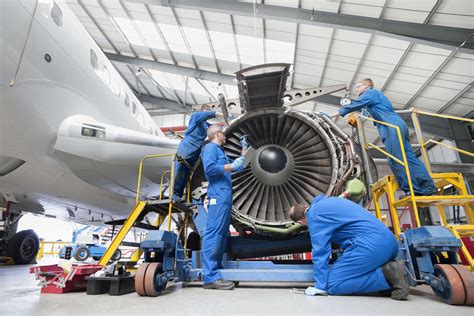
Frequently Asked Questions
What is 3D printing, and how does it work?
+3D printing is a manufacturing process that builds components layer by layer using a digital model. It works by melting and fusing together materials, such as metals, plastics, and ceramics, to form the desired shape.
What are the benefits of 3D printing in aerospace?
+The benefits of 3D printing in aerospace include reduced material waste and energy consumption, increased precision and accuracy, improved component performance and reliability, and reduced production time and cost.
What is the future of 3D printing in aerospace?
+The future of 3D printing in aerospace is promising, with many companies investing heavily in research and development. As the technology continues to advance, we can expect to see more widespread adoption of 3D printing in aerospace manufacturing.
In conclusion, the successful printing of the titanium engine component by Lockheed Martin marks a significant breakthrough in the adoption of 3D printing technology in the aerospace industry. As the technology continues to advance, we can expect to see more innovative applications of 3D printing in aerospace manufacturing.