Intro
Discover the art of MIG welding stainless steel with our expert guide. Learn the top 5 ways to achieve strong, corrosion-resistant welds, from choosing the right shielding gas to optimizing your welder settings. Master techniques for welding stainless steel tubes, pipes, and sheets with precision and ease.
MIG (GMAW) welding is a popular process for joining stainless steel due to its high productivity, ease of use, and good weld quality. However, MIG welding stainless steel can be challenging due to its unique properties. Here are five ways to MIG weld stainless steel:
Stainless steel is a versatile material that offers excellent corrosion resistance, making it an ideal choice for various industries, including food processing, pharmaceuticals, and construction. When it comes to welding stainless steel, MIG (GMAW) welding is a widely used process due to its high speed and ease of use. However, MIG welding stainless steel requires careful consideration of several factors to achieve high-quality welds.
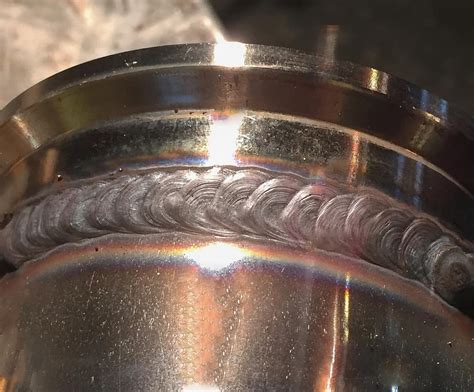
Understanding the Challenges of MIG Welding Stainless Steel
Before we dive into the five ways to MIG weld stainless steel, it's essential to understand the challenges associated with this process. Stainless steel has a high thermal conductivity, which can lead to a slower cooling rate and a greater risk of distortion. Additionally, stainless steel is more prone to porosity and lack of fusion due to its high nitrogen content.
Way 1: Choosing the Right Shielding Gas
The choice of shielding gas is critical when MIG welding stainless steel. The most commonly used shielding gases for MIG welding stainless steel are:
- Argon (Ar)
- Helium (He)
- Carbon dioxide (CO2)
- Tri-mix (Ar + He + CO2)
Argon is the most widely used shielding gas for MIG welding stainless steel due to its ability to provide a stable arc and a smooth weld pool.
Way 2: Selecting the Right Wire Feed
The wire feed is another crucial factor when MIG welding stainless steel. The wire feed should be compatible with the base material and the shielding gas. Some common wire feeds used for MIG welding stainless steel include:
- ER308L (low-carbon stainless steel)
- ER308 (stainless steel with a higher carbon content)
- ER309L (low-carbon stainless steel with a higher nickel content)
The wire feed should be chosen based on the specific requirements of the project, including the base material, the desired weld properties, and the equipment being used.
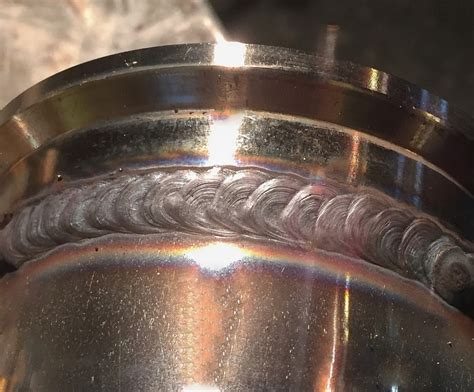
Way 3: Optimizing the Welding Parameters
The welding parameters, including the voltage, current, and travel speed, play a critical role in determining the quality of the weld. The welding parameters should be optimized based on the specific requirements of the project, including the base material, the wire feed, and the shielding gas.
Some general guidelines for optimizing the welding parameters include:
- Voltage: 16-22 volts
- Current: 100-250 amps
- Travel speed: 10-20 inches per minute
Way 4: Maintaining a Clean and Dry Welding Environment
Maintaining a clean and dry welding environment is essential when MIG welding stainless steel. The welding area should be free from dust, oil, and other contaminants that can affect the quality of the weld.
Additionally, the welding equipment should be properly maintained, and the wire feed should be kept clean and dry to prevent porosity and lack of fusion.
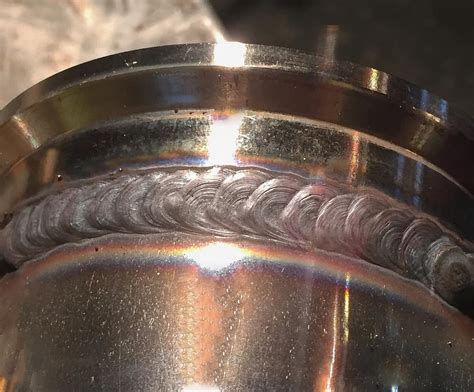
Way 5: Using a Push-Pull Wire Feed System
A push-pull wire feed system can be beneficial when MIG welding stainless steel. This system allows for a more consistent wire feed and a better control over the welding process.
Additionally, a push-pull wire feed system can help to reduce porosity and lack of fusion by providing a more consistent wire feed.
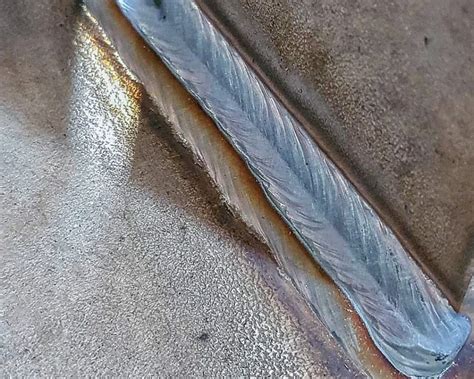
Gallery of MIG Welding Stainless Steel
MIG Welding Stainless Steel Image Gallery
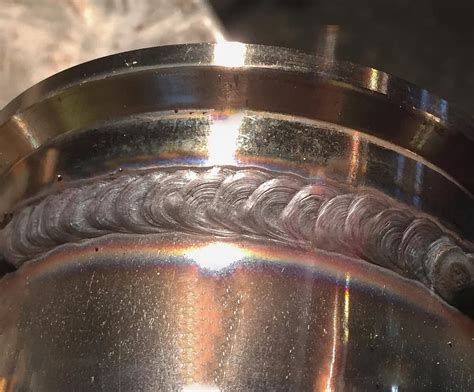
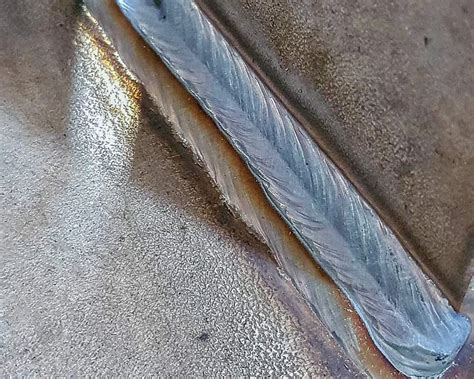
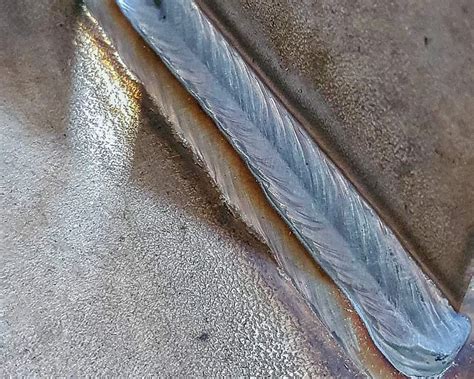
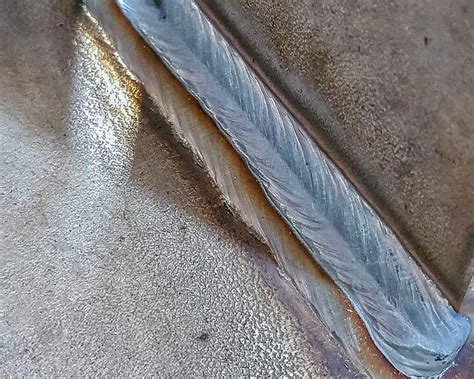
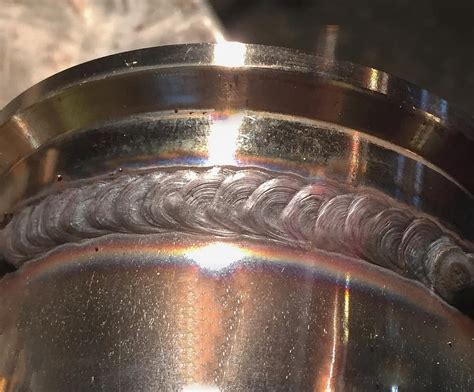
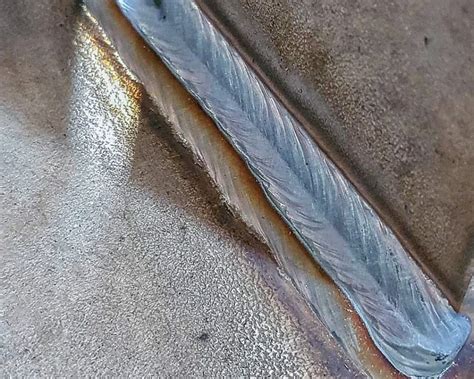
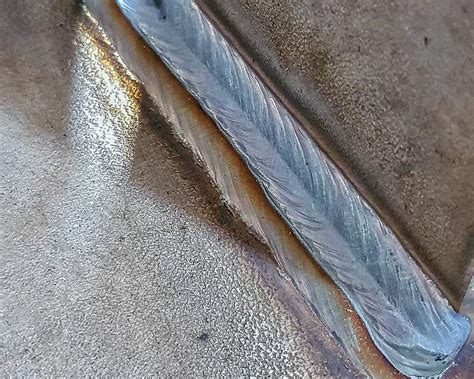
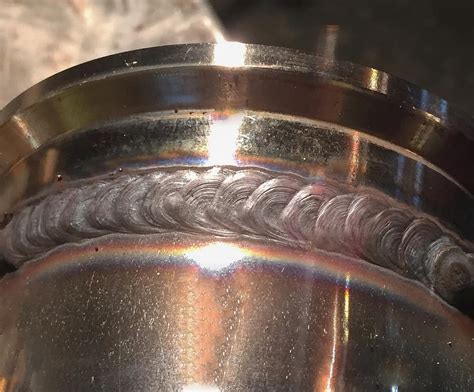
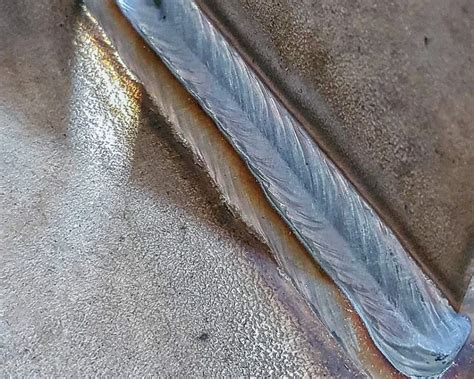
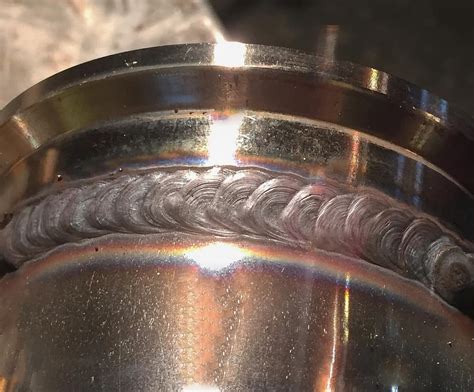
FAQs
What is the best shielding gas for MIG welding stainless steel?
+Argon is the most widely used shielding gas for MIG welding stainless steel due to its ability to provide a stable arc and a smooth weld pool.
What is the recommended wire feed for MIG welding stainless steel?
+The wire feed should be compatible with the base material and the shielding gas. Some common wire feeds used for MIG welding stainless steel include ER308L, ER308, and ER309L.
How can I prevent porosity and lack of fusion when MIG welding stainless steel?
+Maintaining a clean and dry welding environment, using a push-pull wire feed system, and optimizing the welding parameters can help to prevent porosity and lack of fusion.
By following these five ways to MIG weld stainless steel, you can achieve high-quality welds and improve your productivity. Remember to choose the right shielding gas, select the right wire feed, optimize the welding parameters, maintain a clean and dry welding environment, and use a push-pull wire feed system to prevent porosity and lack of fusion.